The importance of fast, reliable internet and phone connectivity was made abundantly clear in the spring of 2020 when hundreds of millions of people across the U.S. and Canada found themselves learning and working at home. According to Deloitte, telecoms have largely held up to surging bandwidth demand throughout the COVID-19 pandemic, but a few notable fiber cuts demonstrated how vulnerable telecoms are to excavation accidents.
Damages to telecommunications facilities have risen year-over-year, according to recent Common Ground Alliance DIRT reports, reaching nearly 205,000 damages in 2019. To find out what it’ll take to reverse this trend, Urbint hosted the panel discussion “Reduce Outages Now: How Telecom and Cable Leaders are Preventing Fiber Damage.” The discussion was moderated by Lindsay Jenkins, Urbint SVP of Strategy and Technical Operations, and featured four top telecom damage prevention experts:
- Anthony Jelniker, Manager of Business Partner Operations, Comcast Cable
- Kent Kildow, Director of Business Continuity and Emergency Management, Verizon
- Matthew Roesner, Director of Network Services for AT&T Field Operations, AT&T
- Jemmie Wang, Partner, AcretivPartners and Task Force Lead, Common Ground Alliance
Read on for the experts’ insights on the true costs of damages for telecoms and their advice on building a best-in-class damage prevention program during rapid 5G expansion.
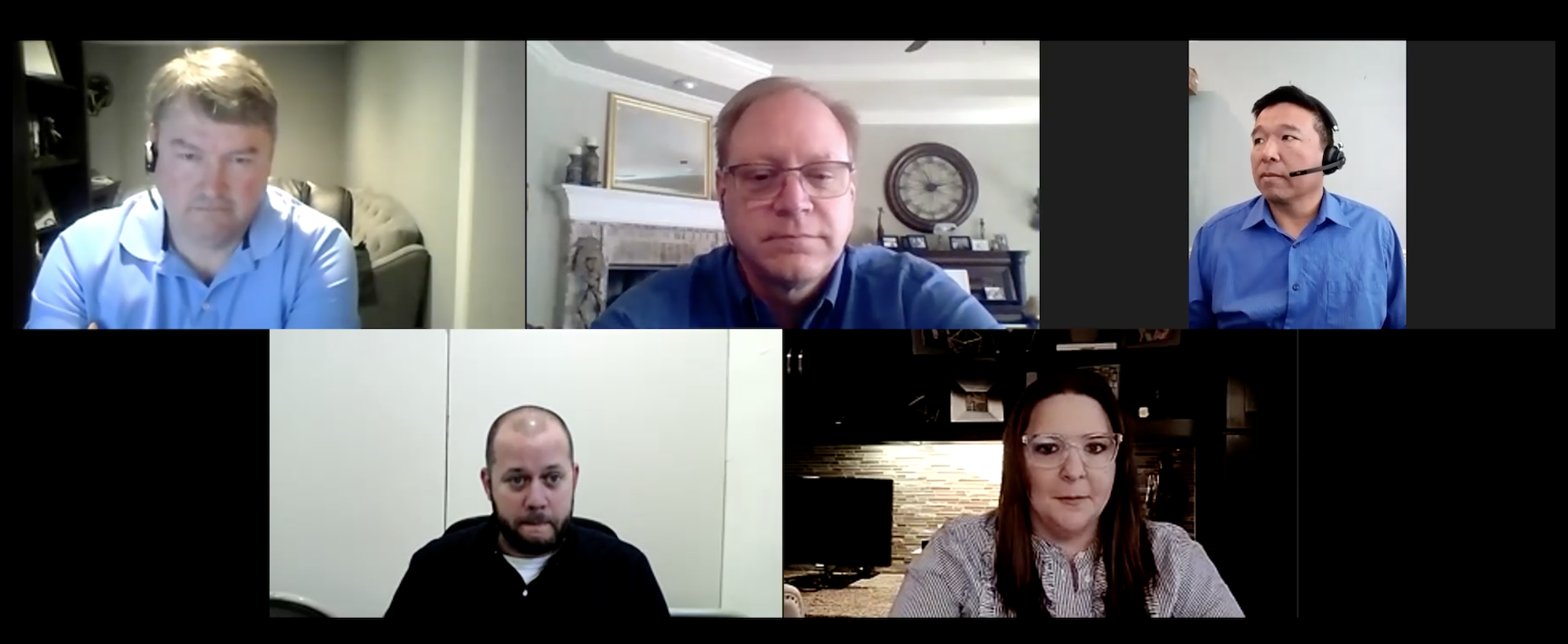
How to build a successful telecom damage prevention program
1. Communicate openly and frequently with damage prevention partners
Preventing fiber optic cable damage requires a coordinated effort between one call centers, utilities, locators, and excavators. All of the panelists emphasized the necessity of strong partnerships with frequent communication between these stakeholders.
“Make sure you have good lines of communication with the 811 centers in your states and that you’re working with them collaboratively to make sure they have the latest information on your assets and to make sure you are getting all of the tickets you should get,” Kildow said.
“We’re all working towards the same goal, and so we really focus on communicating between teams,” Jelniker said. “At Comcast, we don’t use the word contractor when we talk about someone we work with. We call them business partners because that’s our relationship. The only way we’re going to be successful is if we help them be successful, and vice versa.”
Check out: 6 benefits of damage prevention programs for telecoms
2. Consider indirect damage costs
The primary goal of a telecom damage prevention program should be to prevent damages to facilities, yet some focus more on damage cost recovery. This strategy is off-base because the indirect costs of damages significantly outweigh direct repair and replacement costs.
“The indirect costs of damages—customer experience, brand reputation, and business downtime—are about 15 to 30 times that of direct costs. So, for every dollar spent in repairing the damage there's $15 to $30 of additional costs,” he said.
“We've had damages at my company where it can be as low as $425, and we've seen six-figure type damages. You can recover [some of those costs] based on whoever was at fault, but you still lose because of lower NPS scores, customer dissatisfaction, lost business,” Roesner echoed.
The panel experts said their companies recognize this and are shifting their focus to the customer. “The first couple of years when I was in this role, my focus was on collecting after damages. [Now] we focus on prevention,” Jelniker said. “The customer experience [is] paramount for us, so we focus on making sure that our customers are up and they have as few problems as possible.”
3. Invest in automated, predictive technology
The volume of one call and 811 tickets is rising. To keep pace, the panelists advised telecoms to invest in damage prevention technologies that automate manual ticket review processes and identify high-risk excavations.
“Don't just throw more bodies at it, more locators, supervisors, or field examiners. Look at the predictive risk, AI systems,” Wang said.
“People are important to damage prevention, but screening and reviewing tickets should be automated,” Jenkins agreed. “Automate what you can automate, and leave workers to do important, proactive work.”
“I would encourage everyone to look at what automation is available. And don't look at it as a one and done, but an ongoing evolution of your capabilities within your company,” Kildow added.
Investments in new technology can be daunting, especially if you’re operating from a tight budget. But, Roesner said, money spent now will mean money saved later.
“Everyone is concerned about budgets. The thing is, you may save a penny now but then end up spending a dollar later on, so spend the money. You will find that, by eliminating some damages, you can spend money on other things. Now, instead of fixing, you’re installing.”
Check out: An introduction to damage prevention software
4. Push for systematic changes
The U.S. damage prevention system was the first of its kind in the world, but it has changed little over the last 35 years. Wang, who has studied the damage prevention systems of Canada, China, Australia, and more, said all damage prevention stakeholders can benefit from improving the U.S. system as a whole.
“There are a lot of aspects of newer systems that we should look at—not to copy their entire system but aspects of the system. Some stakeholders are not adhering to best practices because the structure of damage prevention in the U.S. is largely the same as it was 35 years ago,” he said. “Look at the structure of the system. If we were creating the damage prevention system from scratch, what might it look like? What aspects of that can we actually implement?”
“We’ve been holding onto this legacy model while, around us, the world has changed. You have new broadband requirements, real-time expectations, increased demand...aging infrastructure, new bills, disparate 811 centers, 70 types of tickets, new regulations, inaccurate facility records,” Roesner said. “Don’t be afraid to challenge the status quo. There are good damage prevention practices in Australia, China, Canada that can be adopted. Let’s be at the forefront of the industry rather than relying on history and the past.”
For more insights on building a successful telecom damage prevention program, watch the panel discussion “Reduce Outages Now: How Telecom and Cable Leaders are Preventing Fiber Damage.”